Demolition isn’t just destruction—it’s the start of something smarter. The moment walls come down, opportunities rise. Rubbish removal shapes not only cleaner spaces but stronger futures. These two forces work together to redefine how we build again.
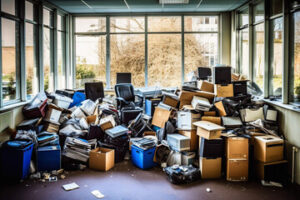
The rise of low-impact demolition prioritizes minimal disruption. Structures are no longer blindly torn apart. They’re deconstructed layer by layer for recovery. Every step now considers noise, dust, and public safety. Click Here to learn more.
Advanced scanning tools assess structural vulnerability. LiDAR and thermal imaging identify stress points in real time. These tools reduce guesswork in takedown phases. Controlled demolition becomes an engineered sequence, not chaos.
Rubbish removal responds by adapting to tighter timelines. Temporary material holding zones shift with project flow. Load balancing between waste categories maximizes efficiency. Debris is moved based on speed, weight, and downstream utility.
There’s a shift toward on-demand demolition modules. Teams no longer operate in fixed daily plans. Algorithms analyze weather, manpower, and waste bin capacity. Daily demolition is based on predictive conditions, not fixed calendars.
Many structures now include embedded recyclable infrastructure. Flooring systems and wall panels come pre-tagged for sorting. RFID chips assist in tracking removed components. Materials can be traced from removal to repurpose without error.
In vertical demolition projects, space is more valuable than speed. Deconstruction proceeds from inside out, not top-down. Internal waste chutes and modular elevators carry debris down. This protects the façade while clearing the core.
AI-driven cameras document everything as it happens. These cameras assess material status and damage levels. Automated logs remove the need for human reporting. Transparency becomes immediate and immutable.
Some demolition tools now include sensor-integrated blades. These can detect tension, moisture, and impact risk while cutting. Smart saws avoid damaging materials meant for reuse. Precision tools create fewer splinters and more salvage.
Waste handlers now wear biometric gear. This gear monitors fatigue, air quality, and muscular strain. It ensures staff safety while aligning with health protocols. Work cycles adjust based on real-time human limits.
Drone-assisted sorting has become part of larger sites. Flying drones scan bin contents and recommend redistribution. These alerts prevent overflows and cross-contamination. Cleanup becomes a continuous loop, not a final phase.
Rubbish removal trucks are now partially autonomous. These units calculate optimal pathing and avoid traffic peaks. Some operate in sync with demolition teams via app triggers. Coordination eliminates wait times between pickup and removal.
Modular fencing for demolition areas includes waste sorting lanes. Workers discard items along designated routes. Material flows are tracked through embedded ID tags. Recycling begins at the moment of removal.
Sustainable demolition considers urban biodiversity. Roof gardens, soil beds, and living walls are relocated first. Protected fauna and flora are boxed and transplanted. Rubbish removal now includes saving what grows alongside steel.
3D printing helps pre-build post-demolition features. Recovered materials are turned into bricks or tiles immediately. This reduces new production needs during reconstruction. Demolition becomes a bridge to restoration, not a break.
Noise-regulated demolition gear is standard in sensitive zones. These machines operate at lower decibel thresholds. Night demolitions now occur without disturbing surrounding homes. Soundless breakdown is now technologically feasible.
In water-locked properties, floating demolition platforms are used. These barge-based systems isolate hazardous elements. Waste is lifted from the site and sent directly to marine-access recycling hubs. Land strain is reduced through waterborne logistics.
Post-demolition dust is now filtered through vertical mist corridors. These structures surround a site perimeter. As dust rises, it’s drawn into ionized chambers for capture. The surrounding air remains breathable throughout.
Certain demolition permits now require post-removal soil testing. Heavy metals and synthetics must be identified. Results dictate how soon reconstruction can begin. The land’s health is now part of the project timeline.
Rubbish removal services incorporate social inclusion programs. Discarded furniture and tools are refurbished for community use. Local artisans sometimes upcycle waste into products. Waste becomes economic value when properly redirected.
Time-sensitive demolitions use light-reactive markers. Painted indicators on walls glow under specific wavelengths. This ensures precise cuts during low-light or emergency teardowns. Visibility and accuracy are always aligned.
Demolition robots are trained on site-specific behavior. They navigate around columns, pipes, and elevation changes. They also communicate with each other via mesh networks. Swarms of robots now perform demolition faster than any crew.
Rubbish removal apps now let clients rate the environmental efficiency. They see how much was recycled, reused, or stored. Transparent results improve trust and refine future workflows. Metrics are no longer hidden in final reports.
Demolition near schools or clinics includes layered acoustic shells. These inflatable barriers cancel out vibrations and sound. They wrap the structure like insulation during teardown. Sensitive zones remain unaffected by chaos next door.
Some removal teams now work in silent zones using sign-based coordination. This eliminates shouted commands and confusion. Nonverbal workflows reduce stress and increase precision. Visual language becomes a demolition standard.
Recyclable waste bags are embedded with biodegradable color codes. These dissolve during industrial sorting. The coding system assists AI-sorting arms to prioritize. Even bag material supports better landfill diversion.
Data from demolition sites helps optimize new building design. Architects review how materials held up over time. This feedback loop strengthens the next structure. Rubbish removal tells stories of success and failure both.
Even foundation removal is now guided by ultrasonic mapping. Subsurface voids and roots are mapped before any digging starts. This prevents collapse or accidental sinkholes. Foundation removal respects what lies unseen.
Energy recovery during demolition has become a new stream. Certain materials are sent to facilities for thermal conversion. Waste becomes stored power used in the new build. Circular economy principles guide every phase.
Old wiring is now separated using induction pulling tools. These tools isolate copper from insulation without damaging pipes. High-value components are salvaged with care. Removal is done with both precision and profit in mind.
Demolition that involves hazardous chemicals now begins with vapor neutralization. Air is treated with compounds that block toxin release. This contains spread before actual wall removal. Health risks are reduced dramatically.
Some companies use demolition simulations in VR before actual work begins. This helps workers visualize risk zones and exit routes. Practice sessions in virtual sites build real confidence. Digital rehearsal improves physical safety.
Rubbish removal scheduling now adjusts by satellite-linked weather alerts. If storms are detected, hauls are rescheduled in advance. Loads are kept dry and secure until safe to move. Rain no longer delays projects unpredictably.
Demolition on heritage-adjacent zones now uses vibration scorecards. Monitors track tremors in nearby historic buildings. If thresholds are breached, tools automatically power down. Preservation works alongside progress.
Energy used in demolition is tracked by project type. Buildings made of glass consume different power than brick. Metrics now determine if methods are justified. This gives clients more power to choose ethically.
Pre-removal inspections include microcrack detection. Structural weaknesses that aren’t visible are flagged. This prevents accidents during partial demolitions. Safety is rooted in knowing what the eye can’t see.
Rubbish removal ends with digital tagging of the cleared site. A site’s post-cleanup status is documented and stored. This information is used by future teams for better planning. Nothing is ever just removed—it’s logged forever.
Demolition teams now collaborate with insurance tech firms. Real-time footage is uploaded for instant damage verification. Claims can be filed while equipment is still on-site. This removes red tape from post-removal recovery.
Cooling corridors are installed temporarily on hot days. These air-conditioned lanes help workers stay cool while clearing debris. Heat is no longer an excuse for slowdowns. Wellness is part of productivity.
In undersea demolition, modular pods trap particles underwater. Debris is floated into sealed tanks for removal to the surface. Marine life is protected from fallout. Even deep-water removals are now clean.
Civic demolition contracts now require community benefit metrics. Noise thresholds, traffic impact, and air quality are scored. Bonuses are paid for minimal disruption. Public good becomes an actual project goal.
Rubbish removal is now broadcast via internal site dashboards. Project managers can monitor haul weight, type, and status. Every load is mapped like a delivery app. Transparency is part of efficiency.
Some companies now use emotional AI to measure worker morale. Facial recognition tracks fatigue, frustration, or focus. Teams receive prompts for breaks or support. Human emotion guides workflow pacing.
Post-removal regeneration includes native seed scattering. Drones drop fast-growing vegetation to stabilize soil. This prevents erosion while plans for rebuilding are approved. Cleanup includes preparation for healing the ground.
As rubbish removal becomes smarter, so does society. Every demolished wall clears the way for better practices. What’s removed no longer vanishes—it transforms. And with each load lifted, the future begins to take form.